Table of Contents
In today's dynamically evolving industrial world, the automation of production processes becomes a key element in providing companies with a competitive edge. Particularly in furniture manufacturing, where precision and quality of finish are extremely important, robotic sanding of chair bases using an industrial KUKA robot reveals its invaluable benefits. This process, combining preliminary sanding, precise surface smoothing, to the final finish, not only ensures high quality and uniformity of products but also increases production efficiency. The use of industrial robots in sanding provides companies with the ability to quickly adapt to changing market requirements, thereby raising their competitiveness on the global market.
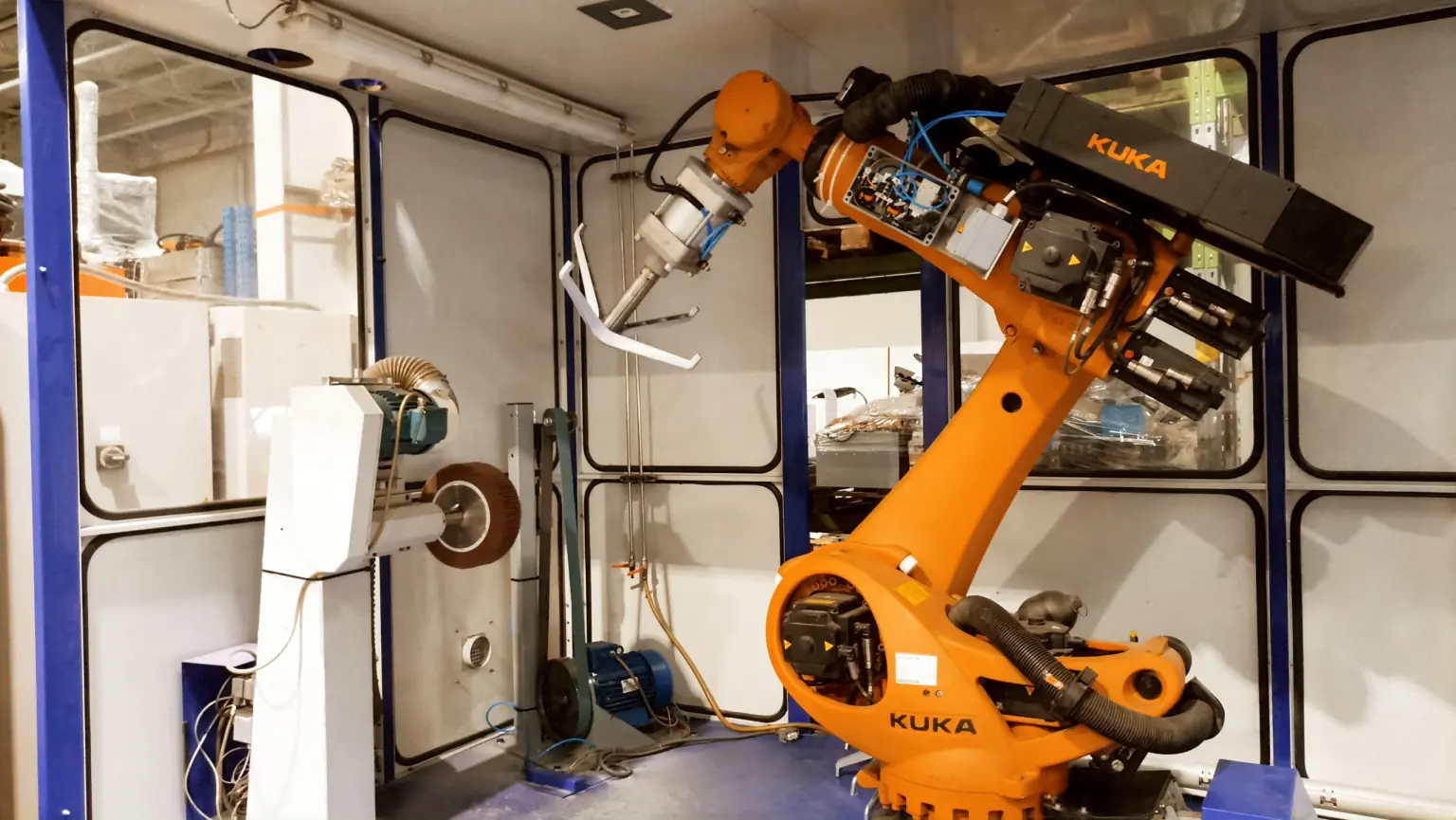
Explore the offer: KUKA Grinding Cell with KR 180 Robot
Arrange a machine demonstration:
Sales Department:
Iweta Włodarczyk EN/DE
Tel. +48 785 198 061
E-Mail: iweta@inter-plast.com.pl
1. Introduction
In the continuous pursuit of optimizing production processes, special attention has been given to the automation of grinding tasks for swivel chair crosses. This project aims to implement a robotic grinding station using the industrial robot KUKA KR 180 R2500 extra, which will significantly increase work efficiency, improve the quality of product finishes, and reduce production costs. Thanks to advanced robotic grinding techniques, KUKA robot grinding, and broad automation of processes, this project represents a significant step forward in the field of automated grinding, highlighting its innovation and technological advancement.
2. Technical Description of the System
The industrial robot KUKA KR 180 R2500 extra is the heart of the robotic grinding station. Its high precision and ability to program complex movement trajectories make it an ideal tool for precise grinding of various materials. Two grinders are used in the grinding process: a belt grinder with a 7.5kW SM-G motor for preliminary grinding and a flap wheel model with a 3kW Weg motor for finishing, enabling high-quality processing of crosses.
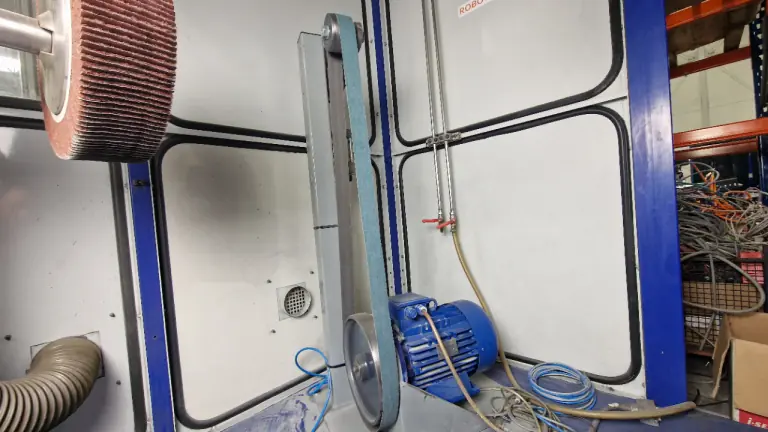
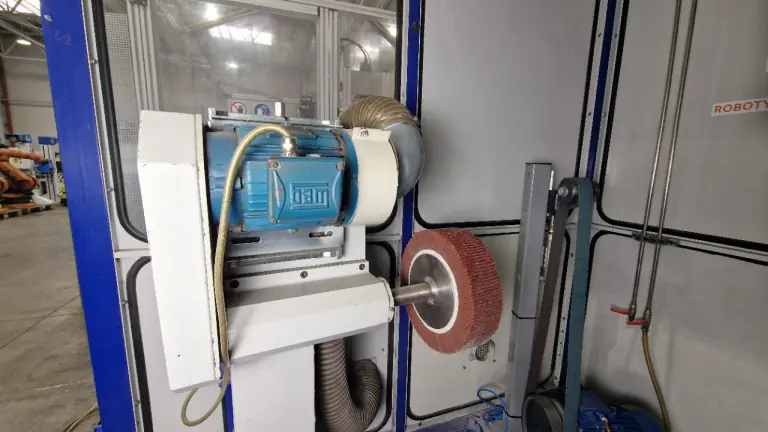
A rotary table ensures smooth transfer of parts between the operator and the robot, thereby increasing process efficiency.
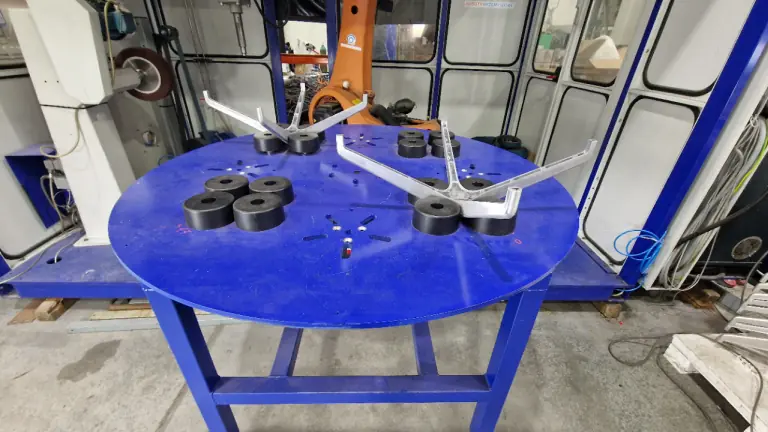
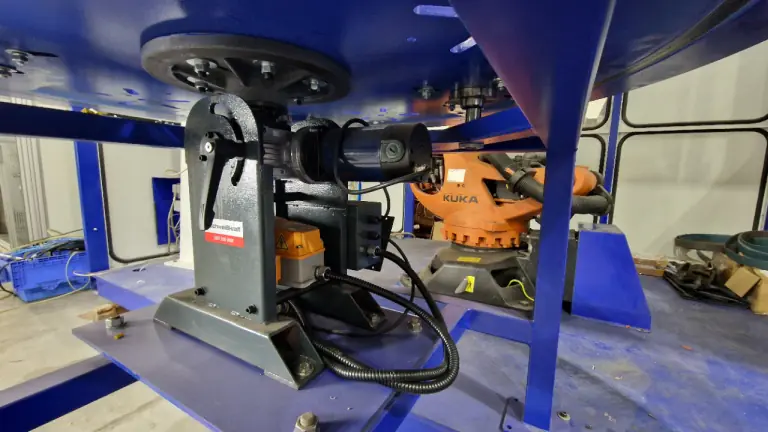
3. Automatic Cross Holder
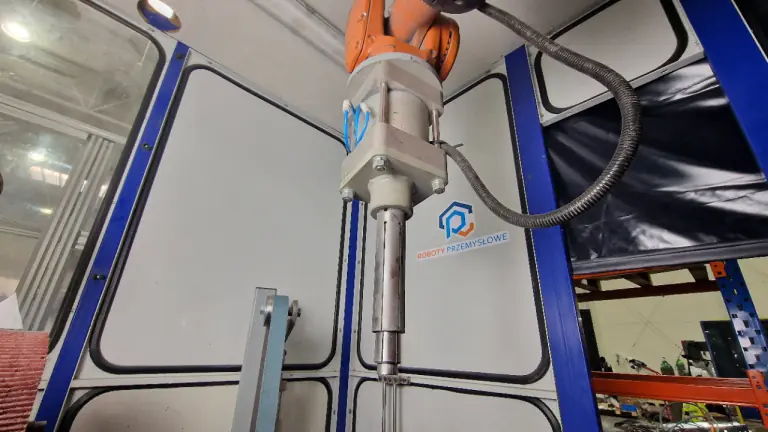
A specially designed automatic holder is a key component that allows the robot to precisely manipulate the crosses. The holder is designed to ensure stable and secure holding of the material during grinding, which is essential for maintaining high quality and precision of processing.
4. Grinding Process for Chair Crosses
The grinding process using the KUKA robot, especially in the context of processing chair crosses, is a complex and precisely designed sequence of operations aimed at achieving the highest quality product finish. This process can be divided into the following stages:
- Preliminary Grinding with a Belt Grinder: At this stage, the crosses are ground using a belt grinder equipped with coarse-grit sandpaper. The goal is to quickly remove any irregularities and prepare the surface for further precise processing. The industrial robot, with its high precision and repeatability of movements, is able to evenly grind the surface of the crosses, which is crucial for maintaining their proper dimensions and shape.
- Precise Smoothing of the Surface using a Flap Wheel Grinder: After preliminary grinding, the process of precise smoothing of the surface using a flap wheel grinder equipped with finer-grit sandpaper follows. This phase is essential to achieve a smooth and uniform surface, which directly affects the aesthetics of the finished product. The robot, controlled with great accuracy, precisely guides the crosses through the grinding zone, ensuring a uniform finish.
5. Safety and Ergonomics of the Workstation
Ensuring safety at the workstation with the industrial robot KUKA KR 180 R2500 extra is a priority. To protect operators and technical staff, a system of light barriers has been implemented as an integral part of the safety measures. Light barriers are strategically placed around the working area, creating an invisible shield that immediately stops the robot's movement if human intrusion into the hazardous zone is detected. This advanced form of protection not only provides a high level of safety but also allows for easy access to the working area for maintenance and technical service without the need to completely shut down the system.
Additionally, the ergonomic placement of workstation elements, such as grinders, the rotary table, and the robot control panel, contributes to improving the comfort of the operator. As a result, operators can efficiently manage the grinding process while minimizing the risk of overloads and injuries related to work. The introduction of light barriers as a safety system component is an important step towards eliminating workplace accidents and raising overall safety standards in the workplace.
6. Process Automation and Production Optimization
The implementation of advanced technologies, such as force sensors and precise robot motion control, allows for continuous monitoring and adjustment of the grinding process, resulting in reduced production costs and guaranteed high quality. Automating the grinding process is a key step towards increasing the efficiency of production lines and enhancing global competitiveness. The integration of all automation components is managed by the KUKA KRC4 control, which is characterized by its intuitiveness, flexibility, and ability to precisely program robot movements. These advantages of the KRC4 control enable quick adaptation to changing production requirements, while ensuring high precision and repeatability of the grinding process.
7. Conclusion
The robotic grinding station for chair crosses, using the KUKA KR 180 R2500 extra robot, represents a breakthrough in production processes. Thanks to the application of the latest technologies and automation, this project paves the way for significant production optimization, cost reduction, and ensuring the highest quality products.